
- #Shapeoko Grbl Controller Laser Software Integrates Well#
- #Shapeoko Grbl Controller Laser Code I Attached#
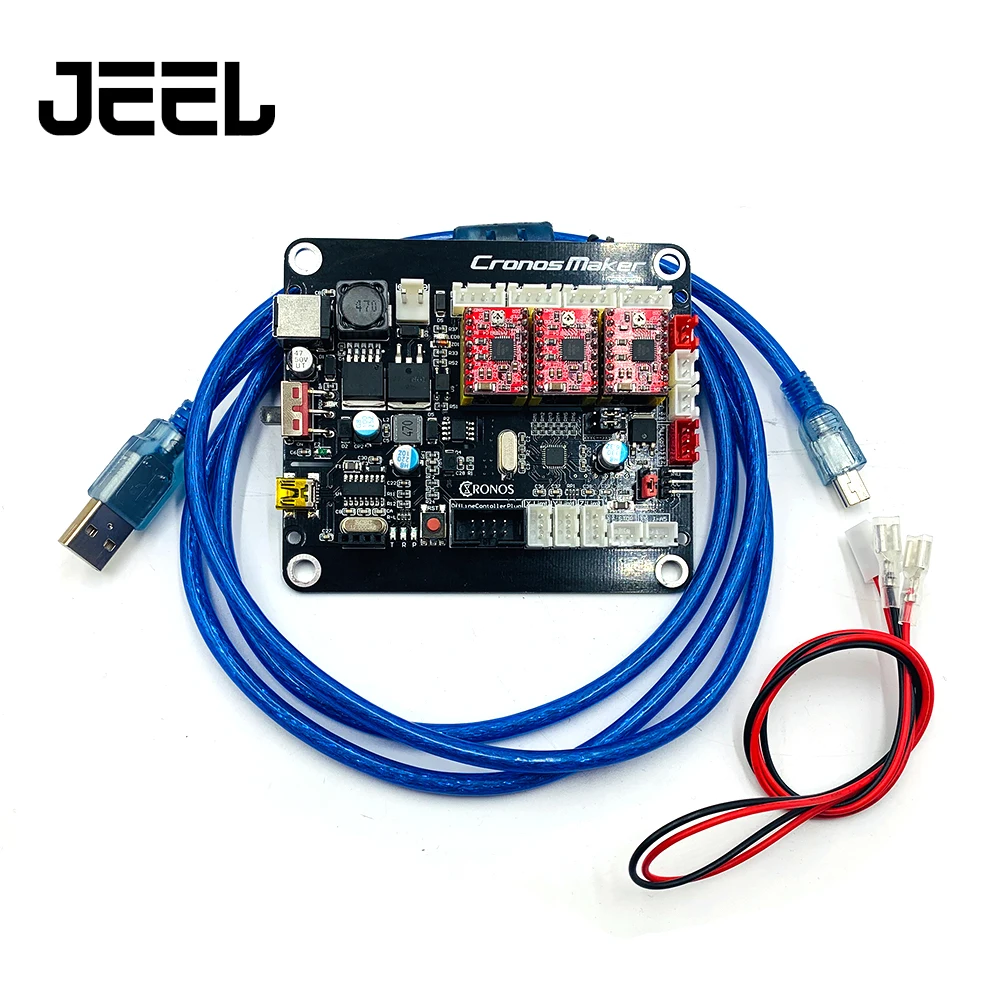
Shapeoko Grbl Controller Laser Code I Attached
As you can see from the Gcode I attached, this may work for vectors but not rasters which give the bit-by-bit commands. Essentially, this M3 command is sent followed by an S0 to give the laser zero power and in each following line, the motor commands are given with an S command for laser intensity. The problem is that Marlin seems to need an M3 command every line in order to change the laser's intensity.As it is now, the Gcode runs with no laser and when I manually add M3 to every line after the start, it runs just fine. Shapeoko, XCarve, and other negative workspace systemsI built a Shapeoko model 3D printer/CNC running off Arduino Mega and Ramps 1.4, configured with Marlin and GRBL interchangeably.
That's almost an inch extra compared to the X-Carve.The higher clearance implies there's more space for working on thick stock and also more space for changing bits.With either machines you have the option of buying "Z-axis kits" which will further increase the Z travel.The higher cutting area, higher Z travel and higher gantry height make the Shapeoko 4 the clear winner in this section.This is called a belt drive and the belts on the X-Carve are 6mm wide (2GT belts).The belts push against the V-Wheels, which roll inside the V-rails on the makerslide extrusion.The rolling V-wheels ultimately move the gantry.X-Carve uses a belt drive for X, Y and Z axes.In the case of Shapeoko, belt drive is used for X and Y axes. X-Carve Size DrawingNote that you will need some depth for the bit, so you cannot engrave a piece that's 67mm thick on the X-Carve.If you want more work area, Inventables also offers X-Carve Pro for businesses, which comes in 4'x2' and 4'x4 sizes.In the case of Shapeoko 4, the gantry height from the work bed is 90mm (3.5"). So that's the maximum thickness of the piece that you can place on the bed. Ideally you want a higher cutting area to footprint ratio.While both these machines will need a relatively large work desk, the Shapeoko 4 has a 3" extra workable length in each of the axes.Z travel is ½" more in Shapeoko 4 compared to X-Carve.Maximum thickness of piece that you can through-cut on the X-Carve is 1.25".The height of the gantry from the bed is 67mm (2.64") on the X-Carve.
Shapeoko Grbl Controller Laser Software Integrates Well
If you want the Pro version, you need to buy it separately, which is a disadvantage.Carbide Motion controller software integrates well with most software such as Carbide Create, Fusion 360, MeshCAM and others. It helps you do quick and simple 3D models which are common in woodworking.If you want a complex intricate model, you'll need to design it elsewhere and bring it into Carbide Create.X-Carve comes included with an Easel Pro license for 3 years.Shapeoko 4 only gives the Carbide Create (free) software when you buy the machine. Inventables doesn't have any official videos of the X-Carve working on aluminum.Even when the X-Carve is used to mill aluminum, the depth of cut needs to be much lower compared to the Shapeoko 4.Note that I have compared the stock machines of both CNCs.It is possible to get better results on the X-Carve by upgrading components such as the belts and Z axis by paying extra.Milling steel on the X-Carve is almost impossible.In conclusion, both machines can cut non-metals well, but the Shapeoko 4 is much better at milling aluminum and metals in general.The clear winner in this section is the Shapeoko 4.Material Capability: X-Carve vs Shapeoko 4The router that you get with the X-Carve fully loaded bundle is the Dewalt 611.Dewalt 611 has a 1.25 hp motor with an RPM that can be adjusted in the range 16,000-25,000.It also has a light under it and that's handy.For using 1/8" diameter bits you need to buy DeWalt 611 Precision Grade Collet and Nut as an add-on from Inventables.Only 1/4" bits fit in the default router collet provided with Dewalt 611.Carbide 3D provides its own router called Carbide Compact Router.It's a stripped version of the traditional router which removes all non-essentials and retains only what's needed for CNC routing.Carbide Compact router has both 1/8" and 1/4" precision collets provided with the default package and so you don't need to buy any add-on to use 1/8" bits.Note that it's possible to mount a Makita RT0701C on the Shapeoko 4 (XXL).The lower RPMs on the Carbide Compact router compared to the Dewalt 611 are really useful for some jobs where you need to go slow.The fact that you need to buy an add-on to use 1/8" bits with the X-Carve is a bit annoying, to be honest, considering the popularity of that bit size.However you can only model 2D and 2.5D designs in Easel.2.5D refers to being able to add depths without really being able to freely model in the Z direction.Because its cloud based, you need an active internet connection at all times to use the software.Since you need the software at all times, to run the X-Carve you need an internet connection.Carbide 3D uses the Carbide Create software for modelling(CAD) and toolpath generation (CAM).For Control and simulation you have the Carbide Motion software.Carbide Create runs on your computer and is not a cloud based software and that's a good thing if you work in area where the WiFi signal is unreliable like a basement.Also, Carbide Create works on Windows OS and Mac OS both which is rare amoung non-cloud software programs.Just like Easel, Carbide Create can only do 2D and 2.5D modeling and toolpath generation.For 3D toolpath generation, Carbide 3D recommends using MeshCAM which is a paid CAM software made by GRZ software.But even if you buy MeshCAM, you miss out on 3D modelling with Carbide Create (free).However, Carbide 3D offers the Carbide Create Pro software which can do 3D modeling and 3D toolpath generation along with everything that the Carbide Create (free version) can do.Carbide Create Pro is not a full-fledged 3D modeling software like Fusion 360 though. CNCBelt Drive in X, Y, and Lead screw in Z-axisLinear Motion comparison X-Carve vs Shapeoko 4Also, Carbide 3D has a number of videos showing you how to mill aluminum and steel with the Shapeoko.Another point to note is that, most of those videos by Carbide 3D are done using the Shapeoko 3, and Shapeoko 4 is a stiffer, better much upgraded version of the Shapeoko 3.This means Shapeoko 4 is even better at milling metals compared to Shapeoko 3.Inventables mentions that the X-Carve can mill aluminum (6061) and they don't advertise it much.There are fewer people who mill aluminum with X-Carve compared to Shapeoko.This comes down to the rigidity and overall power of the X-Carve. Backlash is likely to occur at high speeds in general.Again, X-Carve offers a belt upgrade but since we are reviewing the stock machines, I haven't considered that.Just like the X-Carve, Shapeoko 4 also uses V wheels for moving the gantry.However, Shapeoko 4 uses leadscrew drives in Z-axis.Leadscrews are generally more accurate than belts however they can be a bit slower.In Z-axis since the distance to be covered is much less than X and Y axes, you want it to be screw-driven rather than belt-driven.Although a ball screw drive would have been better in the Z axis, a lead screw drive is better than a belt drive.Overall, I'd say the Shapeoko 4 wins again due to the better belts and the leadscrew driven Z-axis.
...
